How ERP System Bridges Information Gaps Across Departments
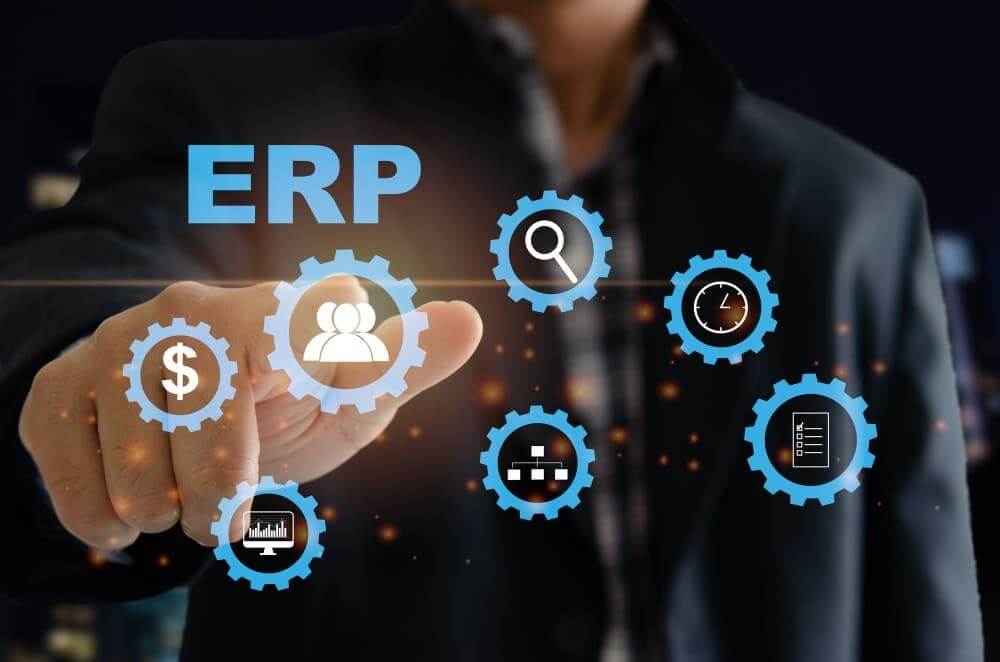
What is an ERP System?
Enterprise Resource Planning (ERP) system is a centralized web application that enables business owners to have a comprehensive, real-time view of every departmental function at the click of a button. From sales, procurement, production, and finance to distribution and marketing, information from every department is easily accessible through the automation of essential business processes, guaranteeing transparency and absolute control over all business operations.
Implementing an ERP system gives a 360-degree view of business operations with data consolidation and seamless flow of information, besides addressing data security concerns looming organization-wide. Let’s find out why a lack of information is harmful to business growth and how an ERP system fills in information voids by facilitating a two-directional flow of information and promoting effective collaboration among departments.
Lack of Clear Information Reduces Business Productivity
For most organisations, seamless collaboration among departments is increasingly becoming complicated due to lack of information. Planning and monitoring day-to-day operations becomes challenging with fragmented information in multiple departments and multiple tools. It leads to:
Inaccurate Decisions
Due to the lack of a centralised data platform to manage and view real-time information from all departments, businesses risk making wrong or inaccurate decisions on resource planning and allocation, which can significantly increase costs to the company.
Ineffective Collaboration
Inter-departmental teams cannot work to their full potential until they are fully aware of the progress the other department is making. Lack of information causes unnecessary delays in project implementation, decreasing employee efficiency and morale.
Operational Inefficiency
Alignment among people, processes and technologies is crucial to improving operational efficiency. Information in ERP forms the digital backbone of a business. Without adequate information access, business output takes a hit, slowing down the entire supply chain and operations.
Workforce Limitations
In the absence of a cohesive data platform, the employees are busy coordinating through calls, emails, and exchanging messages with vendors and other departments to get information updates, leading to a waste of time that could otherwise be devoted to core business functions.
High Response Time
Clients, partners and stakeholders don’t have the patience to wait for order updates and delivery. Lack of visibility into the production pipeline or shipping information can easily frustrate them, harming business relationships.
Also Read: How Can Small-Scale Businesses Ensure Tech Support?
Information Silos
With data scattered across departments in software specific to each department, data integration becomes a laborious task. This often leads to lost opportunities and increased costs for the organisation.
How do ERP System Enable Smooth Information Flow?
The opportunity to use ERP to bridge the information gap helps improve the organisation’s performance and assure a business of its growth through perfectly aligned coordination among departments. Following are the key benefits of implementing ERP.
Two-directional Information
Traditionally, organisations have followed a unidirectional flow of information model, starting with suppliers’ data and ending with shipping and delivery information. In the process, each department concerned itself with information relevant to its department only, without the need for a collaborative framework to achieve common business goals. With ERP software, on the other hand, each department gets real-time visibility into another department. The procurement team knows exactly which products are selling faster to plan inventory, whereas the sales team can furnish delivery date schedules based on raw material availability.
Centralised Platform
ERP software consolidates data scattered across departments and brings them into a single, unified web application. As a result, businesses can easily monitor data and address the security concerns of stakeholders. Cohesive data integration eliminates the need for multiple manual data entries and duplication, reducing errors and redundancies while tracking the flow of information from procurement to shipping with precision. For example, if the product packaging team is ready with a dispatch order, the logistics team can automatically view the order update through the ERP dashboard.
Streamline Reporting
Finance managers are responsible for ensuring accurate financial reporting and strictly adhering to regulatory guidelines and standards. ERP automates accounting processes across departments and provides finance managers with data access to every department, the performance of which can be instantly visualised through graphs and charts. A detailed analysis of data from various departments enables finance managers to effectively maintain audit trails and mitigate risks. Department heads can further avoid disputes and fix accountability by knowing exactly when data was added or modified.
Manage Inventory
For an inventory manager, minimising storage costs is crucial, and the best way to do so is to avoid overstock. It is also critical to prevent stockouts. Inventory management can be optimised with clear information flow upstream and downstream. Data from sales departments like sales forecasts, promotions, and marketing campaigns allows inventory managers to anticipate finished goods demand. Access to manufacturing schedules helps align raw material demand. Similarly, access to information like raw material delivery time ensures it doesn’t hinder the manufacturing process due to a shortage of raw materials.
Maintain Operational Efficiency
Information lags always make collaboration with others a daunting task, but with ERP automation, sharing information gets smooth and easy. As soon as a salesperson feeds new order details into the ERP, the procurement team triggers action by placing the order for raw materials needed for order fulfilment. In turn, raw material vendors with the necessary permissions to the ERP interface soon get the order update and begin the order fulfilment. Thus, a central data repository triggers information flow throughout the supply chain, drastically improving operational efficiency.
Scale operations
With an ERP application, businesses can gain real-time insights into production capacity utilisation rate, sales volume, warehouse capacity, supplier network, and customer base. A strong grasp of these factors is essential for making strategic business decisions and carefully planning business expansion. Likewise, maintaining flexibility based on demand ensures optimum utilisation of resources. A manufacturer can quickly adapt their business processes to match changes in demand. This seamless end-to-end flow of information in ERP enables them to adjust production volume and product variety with ease.
Wrapping up
Whether it is managing inventory, maintaining operational efficiency, or improving the financial health of the company, access to information from across departments ensures that you do so with a high degree of accuracy and confidence using ERP.
Sage X3 prioritises collaboration by bringing together all departments into a single source of information. Streamline the decision-making process by accessing information from inventory, production, finance and sales to help you communicate effectively with partners, vendors and stakeholders.